In the realm of embroidery, having the right file format can significantly impact the quality and compatibility of your designs. Among various formats, the DST format for embroidery stands out as one of the most widely used across different embroidery machines and software. This article delves into the specifics of the DST format, its origins, advantages, limitations, and its relevance in today’s embroidery landscape.
Introduction to Embroidery File Formats
Embroidery file formats dictate how embroidery designs are structured, stored, and executed on machines. These formats not only determine the quality of your finished product but also play a crucial role in ensuring compatibility with specific embroidery machines. Just as JPEG and PNG formats are essential for digital images, embroidery formats serve a similar purpose for stitch files.
Importance of Choosing the Right Format
Selecting the correct embroidery file format is pivotal for both professional and hobbyist embroiderers. A compatible format ensures smooth operation of the embroidery machine, minimizes the risk of errors during production, and allows for efficient use of the software. Incorrect formats might lead to misinterpretations by machines, potentially resulting in ruined fabric or wasted materials. Understanding the distinct characteristics of various formats enables embroiderers to select the most suitable option for their projects. Clear comprehension of file types also aids in converting designs from one format to another, which is often necessary when purchasing designs online.
Overview of Common Formats (DST, PES, EXP, etc.)
The landscape of embroidery file formats includes several key players, each with unique properties. Among the most commonly used formats are DST, PES, EXP, ART, and HUS. Below is a table that outlines some of the primary characteristics of these formats:
Format |
Developed By |
Max Colors per Design |
Notable Features |
DST |
Tajima |
256 |
Binary format; widely compatible with commercial machines |
PES |
Brother |
127 |
Extensive stitch and color support; popular among hobbyists |
EXP |
Melco |
100+ |
Allows editing and detailed design information |
ART |
Wilcom |
255 |
Best for complex designs; supports formatting options |
HUS |
Husqvarna |
127 |
User-friendly and robust design capability |
These formats are pivotal in defining the capabilities and limitations of the machines using them. As a result, understanding these distinctions is crucial in making informed decisions regarding which format to use for specific embroidery tasks.
What is DST Format?
The DST format, which stands for “Tajima Stitch File,” was developed by Tajima, a leading manufacturer in the embroidery machine sector, in the late 1980s. The format has since become a cornerstone in the world of machine embroidery.
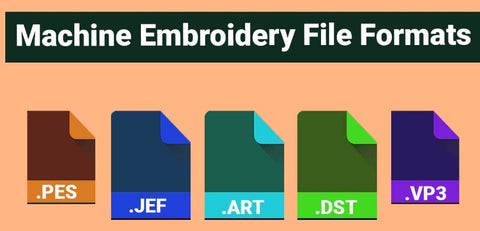
Origin and Development by Tajima
Tajima sought to create a standardized format that would streamline the process of transferring embroidery designs from software to machines. The DST format employs a binary file type, which essentially encodes the necessary stitch data for the machine to execute. As the most commonly used format, it enables manufacturers and digitizers to simplify interactions between design software and hardware.
Over the years, the widespread adoption of the DST format has helped establish it as a trusted choice across both commercial and hobbyist sectors. The capability to produce high-quality embroideries made it a favorite among businesses specializing in embroidery services. Thus, the DST format’s simple structure, when properly utilized, can result in accuracy and efficiency that are highly valued in both professional and individual embroidery environments.
Advantages of DST Format
The DST format comes with several advantages that make it a popular choice among embroiderers and manufacturers.
Widespread Compatibility with Machines
One of the most significant benefits of the DST format is its high compatibility across numerous brands and models of embroidery machines. This universal acceptance makes it an ideal choice for both commercial and home-based operations. Since many embroidery shops utilize machines capable of processing DST files, it ensures that designs can be efficiently shared and utilized across different platforms, ultimately facilitating a collaborative environment within the industry.
Simplicity in Design Encoding
Moreover, DST files employ a straightforward algorithm to encode embroidery designs. Each stitch is defined in relation to its position and type, leading to easy interpretation by machines. This simplicity in encoding means that the files are generally smaller in size compared to more comprehensive formats, allowing for quicker transfers and ease of use when managing large volumes of designs. As a result, embroiderers can efficiently build libraries of DST embroidery designs and streamline their workflow.
Limitations of DST Format
Despite its numerous advantages, the DST format is not without its shortcomings. One of its primary limitations is its restricted color palette. The DST format only supports a maximum of 256 colors per design, which can be highly constraining when working on intricate projects that require vibrant, multi-colored outcomes. This limitation is particularly relevant for designs that incorporate gradients or a vast array of colors; embroiderers may find themselves needing to simplify their designs or adjust to alternative formats.
Another issue with the DST format is its deficiency in more advanced features found in newer file formats. Enhanced functionalities, such as thread type preferences, detailed design information, and multi-directional stitch instructions, are limited in DST. This can be a significant drawback for digitizers and users who seek to create complex designs that require more advanced settings. Additionally, the age of the format means it is less adaptable to the evolving technologies and methodologies in embroidery digitizing today.
As a result, while the DST format remains a staple in the embroidery community, its limitations could necessitate consideration of alternative formats that more effectively cater to advanced embroidery projects.
Restricted Color Palette and Complexity
One of the primary limitations of the DST format for embroidery is its restricted color palette and complexity. Specifically, the DST format traditionally supports a maximum of 256 colors. This restriction can significantly impact the creativity and complexity of the designs that can be produced. While this may seem sufficient for simpler designs, intricate patterns that require subtle color variations or gradients often suffer from this limitation. The complexity of certain designs is often lost when reduced to a mere 256 colors, leading to a less visually appealing final product.
For instance, in intricate floral designs that may use various shades of petals and leaves to reflect natural beauty, a limited color palette can result in a design that appears flat and lacks depth. This lack of nuance is a significant drawback for high-quality commercial embroidery, where the expectation is for designs to have rich details. Furthermore, the reliance on fewer colors means that embroidery digitizers must frequently make compromises, choosing which elements to emphasize in the design, often leading to a less vibrant final product.
Some embroidery professionals opt to supplement DST designs with additional file formats that support broader color ranges when creating more complex projects. Having multiple versions—such as a free DST file for embroidery along with a version in PES or EXP—allows for redundancy and flexibility among different types of embroidery machines and projects.
As businesses look to meet client demands for unique, colorful, and intricate designs, the limitations of formats like DST can be a significant hurdle. It pushes digitizers and embroiderers to adapt by creatively using the available color space or seeking alternative formats that can better meet their design needs.
Lack of Advanced Features Compared to Newer Formats
Alongside its restricted color palette, the DST format also suffers from a lack of advanced features compared to newer embroidery file formats. DST files are often considered “stitch-based,” meaning they primarily contain data regarding the stitches themselves, but lack additional design features. This fundamental design results in limited functionality in comparison to formats like PES or EXP.
The inability to store more detailed design information limits the potential for fine-tuning and customization of the embroidery pattern after the digitization process. For example, unlike newer formats that allow for the manipulation of designs post-creation—such as adjusting stitch types, sequence, or even modifying individual stitches—the DST format provides little flexibility once a design has been rendered. This rigidity can be particularly troublesome in commercial settings where client feedback might necessitate quick alterations to designs.
Moreover, in more advanced formats, it is possible to include additional metadata about the design itself, such as thread type, color codes, or even additional design elements that can be referenced by the embroidery machine. For instance, when dealing with digital embroidery design contracts or larger projects, this data can facilitate better management of corpulent design aspects, promoting efficient workflows that simply aren’t achievable with pure DST files.
Given these limitations, many digitizers and embroidery professionals are moving toward newer formats that offer enhanced features. This trend reflects a growing desire for more versatile design options, which ultimately helps to maintain competitiveness in a rapidly evolving market.
Comparison of DST with Other Formats
When navigating the world of embroidery digitization, understanding how DST stacks up against other file formats is crucial. Below is a comparison chart that highlights key differences between DST and two prevalent formats: PES and EXP.
Feature |
DST Format |
PES Format |
EXP Format |
Max Colors |
256 |
Up to 127 |
Varies based on design |
Design Flexibility |
Limited |
Moderate |
High |
Editing Capabilities |
No |
Limited |
Yes |
Machine Compatibility |
Widely Compatible |
Commonly Supported |
Primarily Melco Machines |
Stitch Information |
Stitch-based |
Detailed (includes colors) |
Comprehensive |
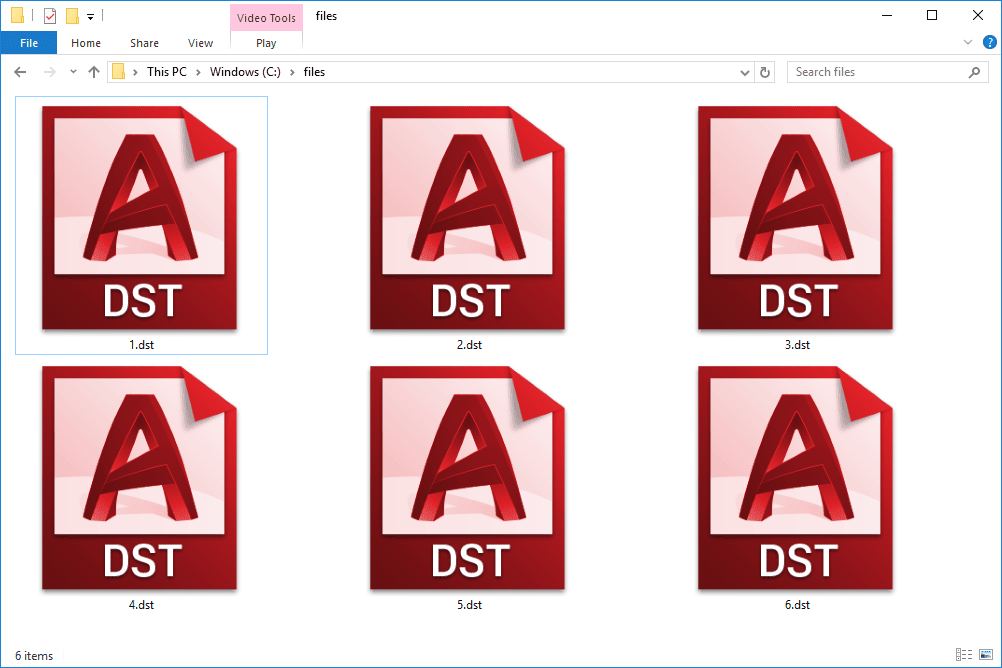
PES Format: Features and Compatibility
The PES format has emerged as a leading choice among embroidery formats, particularly favored for home and hobby use, due to its unique features and compatibility with various embroidery machines.
Enhanced Stitch and Color Storage
Developed by Brother Industries, PES files are tailored for optimal use with Brother embroidery machines but have expanded their compatibility to a wide array of machines from other brands. One of the standout features of the PES format is its ability to accommodate an impressive amount of stitch data—up to 300,000 stitches per design—and support for up to 127 thread colors. This enhanced capacity enables designers to create sophisticated and intricate designs without the limitations imposed by the DST format.
For hobbyists looking to expand their design capabilities, the availability of PES embroidery designs free download can be quite beneficial. A user can access a broad array of ready-to-use templates that leverage this compatibility, making it easier to experiment with high-stitch count designs that incorporate numerous colors. The file structure also allows for straightforward edits, enhancing user experience and creativity when crafting unique pieces.
Popularity Among Hobby Embroiderers
The popularity of PES is further illustrated by its widespread adoption among hobby embroiderers. Many modern embroidery machines—from well-known manufacturers such as Singer and Janome—support PES files, making it one of the most versatile and universally accepted formats available. As a result, hobbyists and small business embroiderers frequently seek out PES designs, often finding communities online that cater to this format.
The PES format’s user-friendly nature allows new embroiderers to engage in complex designs without advanced technical skills. Tutorials and resources, including how to make a DST file for embroidery, often provide pathways for novice users to familiarize themselves with the PES format, enabling them to create intricate patterns without the need for programming knowledge.
EXP Format: Flexibility and Editing Features
The EXP format stands out in the embroidery world due to its flexibility and editing capabilities. Primarily developed for Melco machines, it offers several advantages over the traditional DST format.
Comprehensive Design Information
One of the significant benefits of using the EXP format is its comprehensive storage of design information, which includes details about stitches, color sequences, and even the types of threads used in the design. This extensive information enables embroiderers to replicate desired effects with precision, maintaining quality and visual appeal.
Moreover, designs saved in EXP format are more suited for modifications. For instance, if an embroiders receives feedback that might require selective stitch removal or color adjustments, they can easily implement those changes, unlike DST where modifications are limited once a design is created.
Pros and Cons of Using EXP
While the EXP format has many advantages, it does come with its drawbacks. The primary downside is that EXP files can be significantly larger than DST or PES files due to the extensive data they contain. Larger file sizes may lead to slower processing times on some embroidery machines, particularly older models. However, the trade-off often proves worthwhile for those who prioritize flexibility and detail.
For professionals aiming to produce high-quality embroidery designs or manage larger projects, the EXP format is frequently favored. The ability to download free DST file for embroidery alongside EXP can also offer cost-effective pathways to obtaining designs that work synergistically across different formats.
How to Choose the Right Format for Your Needs
Selecting the appropriate embroidery format hinges on several factors, including the specifics of your embroidery project, machine compatibility, and desired design complexity. Understanding your needs is essential in determining whether to utilize DST, PES, EXP, or another format.
For straightforward designs with limited color complexity, especially those suited for commercial applications, the DST format might be perfectly adequate. It’s widely supported across various embroidery machines, enabling smooth workflows in professional settings where consistency and speed are paramount.
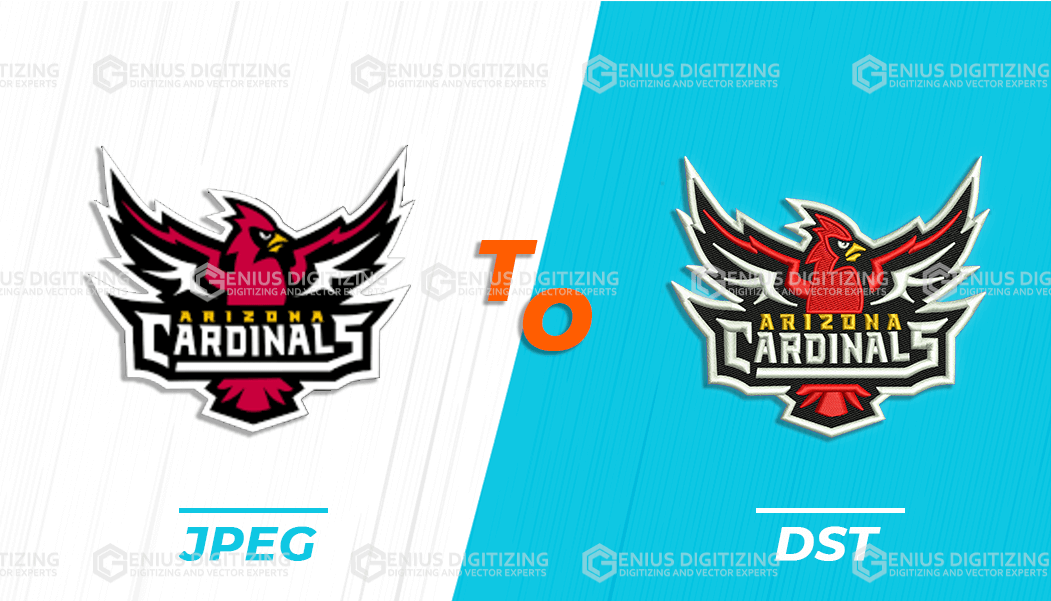
However, if you’re working on projects that demand intricate detail or varied color use, consider the PES or EXP formats. PES offers better color support and editing capabilities while also being compatible with most home embroidery machines. On the other hand, EXP is ideal for more advanced users needing extensive editing options and design flexibility.
Before committing to a specific format, assess your machine’s capabilities and the design requirements. Look for resources that provide insight into how do I download free embroidery designs based on your machine’s supported formats. Remember, each format possesses unique strengths and weaknesses, and the right choice can enhance your embroidery projects, ensuring they align with both your creative vision and operational needs.
Assessing Machine Compatibility
When considering the use of the DST format for embroidery, one of the foremost aspects embroidery professionals must evaluate is machine compatibility. Most modern commercial embroidery machines accept a variety of file formats, including DST embroidery designs, but it is crucial to verify your specific machine’s file compatibility before proceeding with any design work.
The _DST format_, originating from the Tajima brand, is universally known for its compatibility with a wide range of embroidery machines used in commercial settings. Many brands, such as Janome and Brother, support DST files. However, the extent of compatibility can vary based on the machine’s model and year of manufacture. For example, new models might support a wider range of file types, including free DST files for embroidery or proprietary formats like PES or EXP, which have more sophisticated capabilities.
It is essential for embroiderers to consult their machine’s manual or manufacturer’s website to clearly understand which formats are supported. Some machines have firmware updates that increase compatibility with various file formats. Furthermore, sewing software and converters are available for users to change file formats when needed, enhancing workflow efficiency. A practical example would be if a designer creates a design in PES format but needs it in DST for a specific commercial machine. They would use conversion software specifically designed for this purpose.
In a commercial environment, time is often of the essence, and ensuring seamless compatibility avoids delays in production. For hobbyists, while creativity is paramount, ensuring compatibility also streamlines the embroidery process and reduces frustrations arising from incompatible file formats.
Considerations for Design Complexity
The complexity of the design is another critical factor when working with the DST format for embroidery. Unlike some of its contemporary counterparts, the DST file format has limitations regarding design intricacy. While it is suitable for a broad range of embroidery projects, it can be restrictive for designs that demand high levels of detail or a wide color spectrum.
The DST format supports a maximum of 256 colors in a file, which may be limiting for highly detailed designs requiring numerous gradients or shades. An embroidery design with intricate details that rely on fine lines, shading, or multiple color changes may not translate well into this format, potentially detracting from the final aesthetic quality. For instance, a complex floral design with shifting color blends would typically have better results in a format that includes richer color support, such as PES or ART.
Moreover, the DST file format is stitch-based, meaning that it encodes a sequence of stitches directly without retaining information about the underlying artwork. This can be challenging when adjustments are necessary, either due to errors or changes in customer preferences. For instance, if a certain stitch does not appear well or meets customer specifications, making adjustments in the DST format may require going back to the original design and re-digitizing.
For intricate designs, digitizers might suggest using alternatives such as PES or EXP, which provide editable features allowing for dynamic modifications after the initial creation. The ability to manipulate stitches, colors, and layering provides a superior level of detail and customization that many embroiderers now seek.
Additionally, it is vital to consider the tools used for creating and editing the designs. Many advanced embroidery software solutions provide users the opportunity to create designs directly in the DST format or convert between formats while retaining as much detail as possible. Understanding both the limitations and strengths of the DST format is essential in achieving the desired outcome for your embroidery projects.
Conclusion
Recap of Key Points on DST and Other Formats
In summary, the DST format for embroidery serves as a crucial component of the machine embroidery world. Its widespread acceptance in commercial environments, ease of use, and straightforward stitch data make it a go-to format for many embroiderers. However, prospective users must consider their machine compatibility, as not all embroidery machines support the DST format, and sometimes, conversion to more versatile formats may be necessary.
When it comes to design complexity, the limitations of the DST format become apparent. The lack of support for a wide range of colors and its stitch-based nature could hamper the creation of intricate designs. Users should be cognizant of these factors and should keep in mind other formats that might suit more complex requirements better, such as PES or EXP.
Final Tips for Embroiderers Choosing Formats
As you delve into the world of embroidery formats, here are some final tips for making the right choice:
-
Check Machine Compatibility: Always confirm your machine’s compatibility with different formats before designing or purchasing embroidery files.
-
Understand Design Requirements: Assess the complexity of your design and choose a file format that can deliver on the intricacies required.
-
Stay Updated with Software: Utilize embroidery software that facilitates easy conversion between formats and offers comprehensive editing capabilities.
-
Experiment Carefully: If trying to use free DST files for embroidery, make sure to test a small design first to ascertain quality and compatibility with your machine.
-
Seek Professional Advice: Do not hesitate to reach out to professional digitizers or experienced embroiderers for insights on the best practices regarding format selection.
Armed with this knowledge, embroiderers can make informed decisions that will enhance the quality of their work while maximizing productivity and creativity in their embroidery projects.